VAIO Z / VAIO Pro Z開発ストーリー Vol.2:開発者が語る「製造工程」
メイド・イン・ジャパンを掲げ、
長野県安曇野市のVAIO本社工場で製造されるVAIO Z。
製造現場の最前線に立つ技術者たちがVAIOのものづくりを語る。

EMS事業本部EMSビジネス統括部
技術&製造グループ技術課
清水 慎也
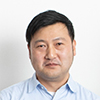
EMS事業本部EMSビジネス統括部
技術&製造グループ製造課
坂本 直樹
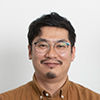
EMS事業本部EMSビジネス統括部
技術&製造グループ技術課
岩下 敬
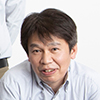
EMS事業本部EMSビジネス統括部
技術&製造グループ実装課課長
中村 康春
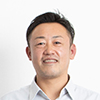
EMS事業本部EMSビジネス統括部
技術&製造グループ技術課
林 哲也
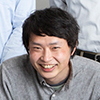
EEMS事業本部EMSビジネス統括部
技術&製造グループ技術課
手塚 毅
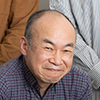
EMS事業本部EMSビジネス統括部
技術&製造グループ技術課
草間 清人
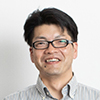
EMS事業本部EMSビジネス統括部
技術&製造グループ技術課
倉科 優一
超・高難度フルカーボンボディ
「これは大変なことになる」
−−まずはVAIO本社・安曇野工場がどういった想いを持って製品を製造しているのかから聞かせてください。
製造技術担当 清水:我々が目指しているのは、お客さまに信頼していただける製品を生み出すための信頼できる現場作り。VAIOでは以前から作業者による官能検査(視覚や触覚など、人間の感覚を利用した品質検査)や手作業による細かな組み立てなど、人の能力を最大限活かすことで得られる信頼を大切にしてきました。
その上で、安定した生産を行うための治具(部品の加工や組み立てをサポートするための器具の総称)であったり、プレス機などの大がかりな設備も独自に設計しています。それによる安定した作業品質、高い精度、細かい作業を実現できることも我々の大きな強みです。人と設備それぞれの特長を活かし、生産品質を高めることが、お客さまの信頼に繋がると考えております。
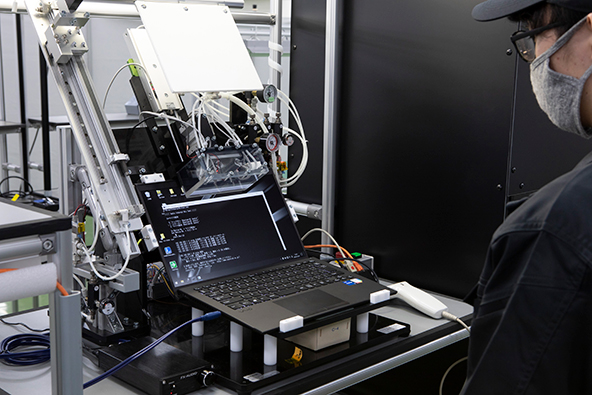
−−一般的に治具は自分たちで作らないものなのですか?
清水:治具を自社設計しているメーカーはあると思いますが、VAIOは特に強いこだわりを持っています。製品のことを隅々まで考慮した治具設計でないと、不整合というか、上手くかみ合わない部分がどうしてもでてきてしまうんです。その点、VAIOでは生産技術のメンバーが製品設計と並行して、治具を設計します。また、そこに作業観点からの要望がタイムリーに反映されるので、できあがると製品にも作業者にもジャストフィットした治具になり、最適な作業品質を実現できます。
生産技術担当 手塚:ちなみに治具には大きく分けて2つの種類があります。1つ目は、その治具がないとそもそも組立ができない、「必要不可欠な治具」。もう1つは、「品質や品位、生産効率を上げるための治具」です。前者は必須なものですので新機種導入の過程で必ず製作しますが、後者の治具については「どうすればより品質良く作り込めるか」といった熟慮を重ね、「こんな治具があれば、より安定した品質で生産ができる!」という結論に至った末に製作が決まるものです。こういった、“こだわりから生まれるアイデアと工夫”が、治具を作る上での重要なポイントだと考えています。
−−その“アイデアと工夫”がVAIOの知見・ノウハウというわけですね。
手塚:そうですね。そして、そういったアイデアと工夫は、製造、製造技術、生産技術、それぞれの視点での気付きから生まれてくるため、関係メンバーが部署を超えて議論をし、気付きを形にしていけるチームワークこそが、我々の強みだと思っています。
−−そうして精度の高い組み立てをサポートする治具が作れるのですね。しかし、そんなVAIOにとっても、今回のVAIO Zの製造はかなりハードルが高かったと聞きます。具体的にはどういったところが難しい製品なのでしょうか?
清水:VAIO Zは天面+ベゼル、パームレスト、ボトムの4面、3枚のカーボンパネルを使っています。その全てに曲げ加工が施されており、曲げの内側の作業が難しい場所に、±0.1mm以内の精度で部品を接着するなど、かなり難度の高い組立てにチャレンジしています。
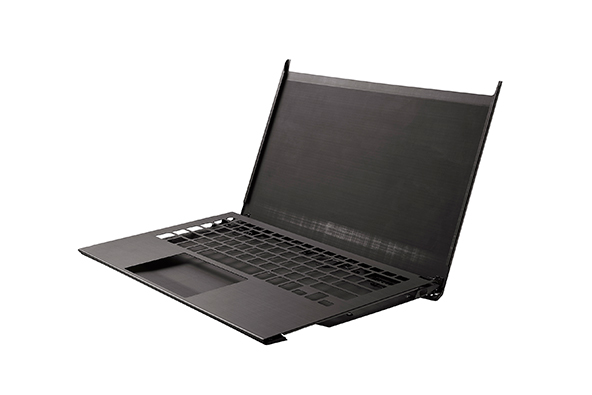
−−その難しさを皆さんが把握したのはいつ頃ですか?
清水:VAIOは「上流設計」と称される、設計の初期段階から製造現場も含めた全工程のメンバーが関わって議論していくものづくりをしているため、我々もかなり早い段階からZをやることは知っていました。当初は皆、すごいものを作れるとワクワクしていました。でも、その後、カーボンを曲げるという話を聞いてびっくり。一転して「これは大変なことになるぞ」と戦慄したのをよく覚えています(笑)。
製造技術担当 林:詳細設計が始まる前から設計、製造、生産技術のメンバーとデザインレビューを実施し、細かな要望を出しながら想定される問題を解決していくようにしました。これまで以上にしっかり情報を共有し時間をかけましたね。いつもの3倍はミーティングをしたのではないでしょうか(笑)。
−−そのミーティングでは具体的にどういうことを話し合うのですか?
林:設計がやりたいことをどうすれば実現できるのかを話し合い、製造するために必要な条件や情報などを共有します。治具を設計するために必要な寸法などのデータもその一つです。たとえばディスプレイ回りでは、部品メーカーから届くカーボンパネルがどのくらいの精度で出来てくるのか、パネルのどこを基準に部品を置いていくのが最適か、センター基準なのか、端合わせなのか、そういったことを細かく確認し認識を合わせながら治具設計や組立作業に反映させていきます。
あり得ない方向からインサート
−−では、実際にどのような仕組み、環境でVAIO Zを作っているのか、製造現場の中からVAIO Zならではのところをピックアップしてお話を聞かせてください。まず、大きなところではディスプレイ回りですね。ここではどういったことをやっているのでしょうか?
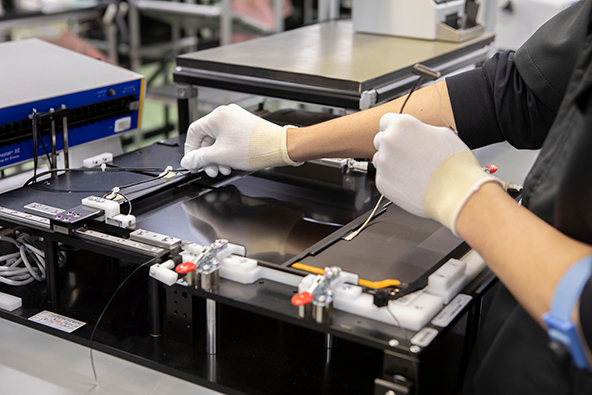
林:一般的な構造のノートPCでは天面パネルとベゼルは別体となっているため、LCDをサンドウィッチするような形で組み立てていけますが、VAIO Zでは天面パネルとベゼルが一体化しているため、横からLCDを滑り込ませるように組み付けなければいけません。しかもLCDの脇にはカメラやアンテナの配線が通っているので、正しい位置から少しでもずれるとケーブルを引っかけてしまいケーブルを断線させてしまう危険性があります。また、組み立て前のカーボンパネルにはわずかに反りがあるため、その状態でLCDを挿入しようとするとLCDに大きな負荷がかかってしまいます。
そこで今回は、カーボンパネルをはめて反りを矯正し、ガイドに沿ってLCDをスライドさせることで、無理なく正しい位置にインサートできる治具を作りました。さらにこの治具にはLCDにかかっているストレスを検知するセンサーを内蔵。カーボンパネルの内部でLCDにどのような負荷がかかっているのかをモニターしながら作業できるように工夫しています。ベゼルの隙間にLCD(液晶パネル)を滑り込ませるなんて組み立て方は、VAIOは勿論、他社製品でも見たことがありません。
生産技術担当 岩下:部品にかかっている負荷を確認しながら組み立てるというのは初めての試み。まずはどうすれば負荷を測定できるのかというところから始めなければいけませんでしたが、いろいろな機材を取り寄せて検証を繰り返し、何とか実現することができました。
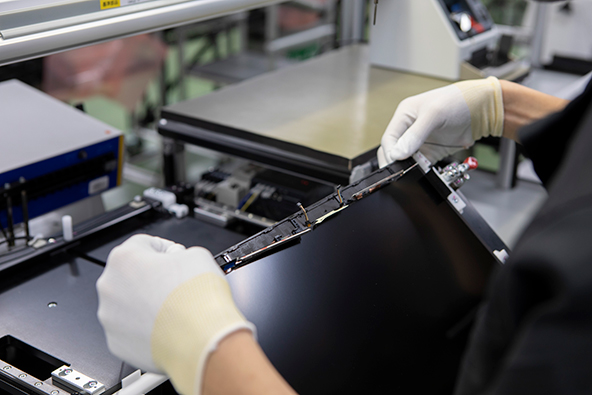
林:次に、アンテナやカメラを固定する樹脂のパーツをカーボンパネルにはめ込んで行くのですが、その際、パネルを固定していた治具が、作業しやすい角度に起き上がるという機能も盛り込むことで、作業が安定し品質向上につながっています。
製造担当 坂本:VAIO Zは奥からスライドさせたり、斜めからビスを打ったり、いろいろな角度から作業をしなければなりません。こうした組み立て方をする製品はこれまでほとんどなかったと思います。今回は、その難しさを治具や設備でアシストすることで、作業者に負担をかけることなく、安定した作業の実現を目指しました。
品質を崩さない生産方法
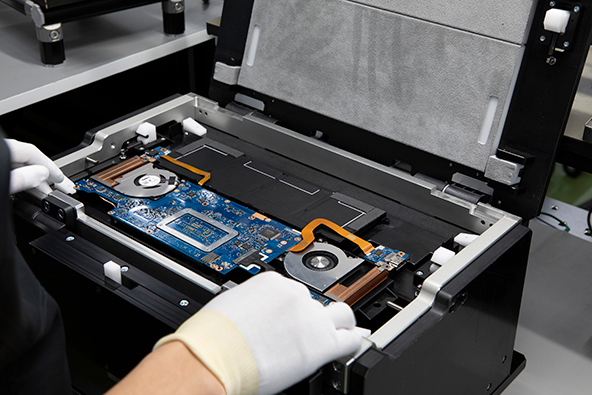
清水:次に紹介するのはVAIO Zのボトム部分です。
通常であれば、各部品をボトムケースに組み付けていくのですが、VAIO Zは基板や放熱部品などパフォーマンスに関係する部品を事前に仮組みし、性能検査した後に、ボトムに移し替える手法をとってます。部品を組み合わせた状態で性能保証し、その組み合わせを崩さずに、製品まで組み上げ再度検査を実施することで、より安心できる品質を実現しております。
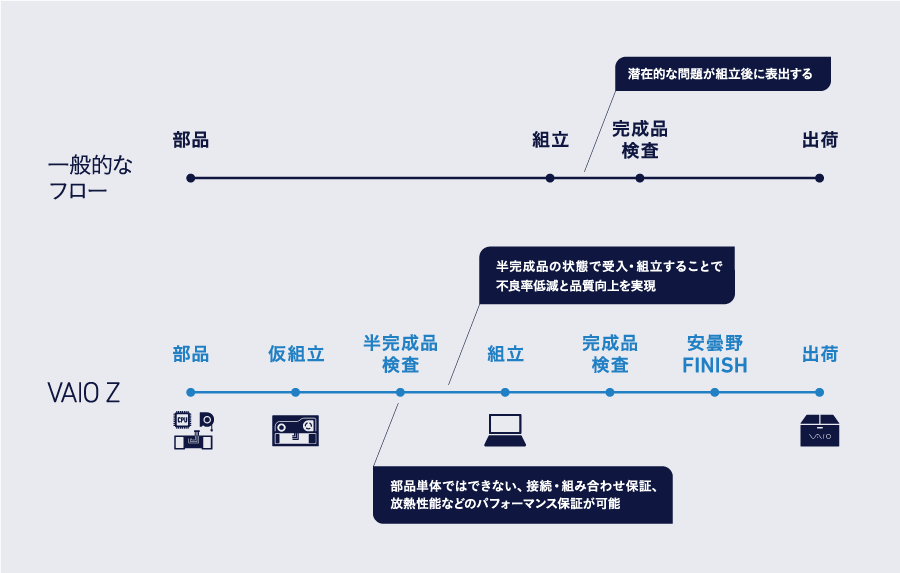
−−仮組みした部品が、その後どのように組み立てられていくのか教えてください
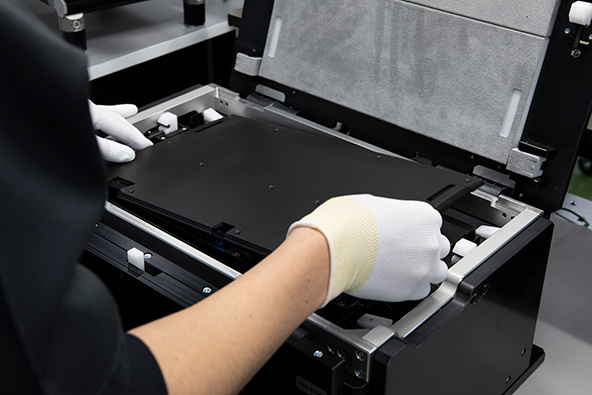
清水:仮組みされた部品にボトムカバーを被せ、治具をぐるっと一回転させます。そこから、フレームを取り除くと、全ての部品がボトムケースに移し替えられます。そうすることで、一度検査をした部品の接続を崩すことなく、品質を維持できます。
手塚:さらに、部品がきちんと取り付けられているかを確認するため画像検査装置にかけるのですが、VAIO Zではこの装置が新しいものになり、これまでの約20倍の速度で検査できるようになりました。しかも検査の精度も大きく高まっていて、部品の有無だけでなく、ケーブルの処理が正しい事なども高精度に見てくれます。
−−精度が上がって、しかも20倍というのはすごいですね。
手塚:ただ、ここで改めてお伝えしておきたいのは、我々があくまで人にしかできない作業を重視しているということ。例えば、カーボンパネル表面の繊維の乱れ、違和感のようなものはどうやっても機械では分かりません。ですので、機械が得意な検査は専用の設備で行い、それによって生まれた時間で人間がしっかりと外観検査などを行う。そういった、人と設備が共存しそれぞれがパフォーマンスを最大限発揮できる生産ラインを念頭に、生産設備を設計しています。
前後左右、高さ。立体的に塗る
−−今回のVAIO Zではボンドの塗布も難易度が高かったと伺いましたが、それらの課題をどう解消したのかについても聞かせてください。これは工程としては、ここまででお話いただいた、LCDのスライドイン、ボトムケースへの部品移し替えの前段階ですよね。
生産技術 草間:そうですね。VAIO Zでは3枚のカーボンパネルを使っていますが、カーボンに直接ビスを打つことはできませんので、樹脂製のビス穴パーツをカーボンパネルにボンドで接着する工程が必要となります。この工程自体は、フラットなカーボン天板を採用している従来モデル(VAIO SX12、SX14など)にも存在するのですが、VAIO Zのカーボンパネルは立体的な形状をしているため、ボンドの塗布が一筋縄ではいかないんです。
−−具体的にはどんな難しさがあるんですか?
草間:ボンドは機械を使って自動で塗布していくのですが、曲げた形状の内側にボンドを塗布するにはカーボンパネルを斜めに傾けなければなりません、するとフラットな部品への塗布時に比べてノズルの「高さ」を考慮しなければならなくなります。
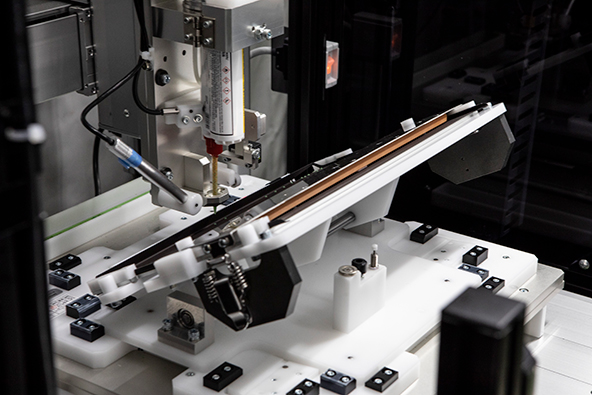
−−「高さ」の調整は、これまでの「前後左右」の調整とは難易度が異なるのでしょうか?
草間:ノズルにはボンドの入ったカートリッジを装着するのですが、そのカートリッジのばらつきで微妙に高さが変わってしまうんです。コンマ数mmというレベルなのですが、VAIO Zではかなり繊細な作業を行っているので、この違いを無視できません。そこで、今回は、最初にカートリッジをセットした後にノズルの高さを調整する機能を追加しています。
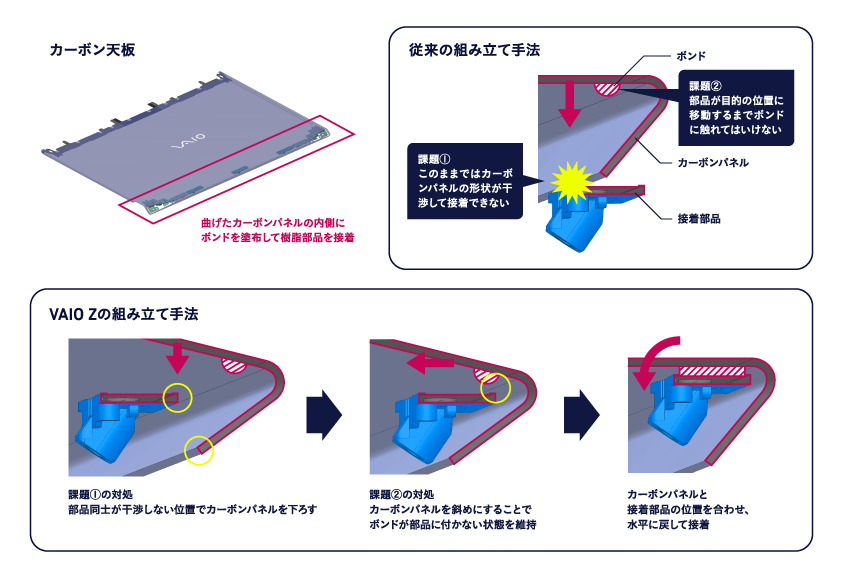
VAIO Zの剛性を実現するためにはボンドの塗布量を減らすことができないが、そのまま組み付けるとボンドが意図しない場所に付着してしまう。そのため部品にボンドが触れない高さでカーボンパネルを浮かせ、そこから角度を2段階に変えながらスライドさせて潜り込ませるように接着位置まで移動させている。接着位置は±0.1mm以内の精度を誇る。
手塚:この他、ボトム部品の接着でも前述したUSBコネクタなどI/O部品の出っ張りによって部品を真上からスッと置けないという大きな課題がありました。ボトムケースを少したわませながら、接着したい部品の上に精度よく置いていかなければならないのです。こういったさまざまな課題を、今まで培った技術と新たな工夫により解決しています。
ここぞという部分は自分たちでやる
−−今回のVAIO Zでは、難度の高い実装(基板にICなどの電子部品を接合する工程)をしているとおうかがいしました。こちらについても聞かせて下さい。
実装担当 中村:VAIO Zでは複数の基板を実装していますが、ここでは電源ボタン一体型指紋センサーについてお話しさせていただきます。この電源ボタン一体型指紋センサーはフレキ基板(フレキシブルプリント基板)と呼ばれるフィルム状の基板の上に狭ピッチのICが載っているという極めて繊細な回路です。これを高品質に、しかも安定して生産するするためには高度な実装技術が必要になります。
−−具体的にどのような実装をされているのでしょうか?
中村:個片で納入されるフレキ基板をアルミ製のキャリアに敷き詰め、実装ラインに流すということをやっています。実はこれは、2015年に発売した先代VAIO Zのマザーボードを実装する際に編み出した技術を発展させたものです。前回は硬質なリジット基板をキャリアに載せて実装したのですが、今回はそれを薄くて柔軟性があるフレキ基板でやるということが大きな違いです。
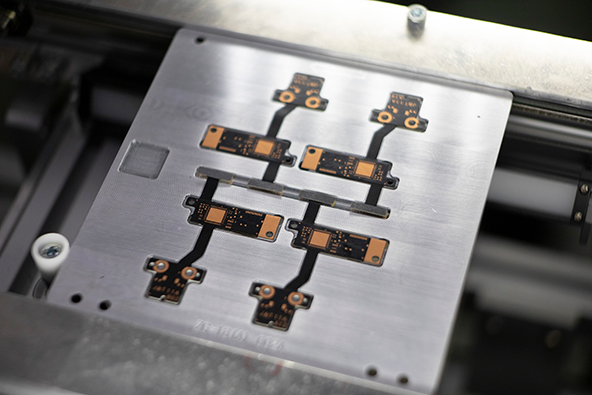
−−フレキ基板をキャリアに載せて実装するというのは珍しいやり方なんですか?
中村:キャリアに載せるまでは他にもやっているメーカーはありますが、狭ピッチのICを個片フレキ基板へ実装しようとしているメーカーは少ないのではないでしょうか。それくらいハードルの高い実装で、やろうと言い出したときは倉科に「本当にやるんですか?」と聞かれたほどです(笑)。
−−具体的にはどういったところが難しいのでしょうか?
実装担当 倉科:実装工程では、キャリアに載せられたフレキ基板表面にはんだを印刷し、そこにICを載せていくのですが、適切な量のはんだを塗布するためにはキャリアとフレキ基板がツライチ(凹凸のない状態)になっていることが好ましいです。ただ、基板の厚さには公差がありますから、それを計算にいれた形状にしなければなりません。また、フレキ基板は人の手でキャリアにセットされるため、貼り剥がしがしやすいよう、ある程度のガタも必要になります。その他、1つのキャリアに何枚のフレキ基板を置けるようにするか、位置決めの穴の位置はどこがいいのか、配置されるフレキ基板はどの方向に向けるのがいいか……さまざまなパターンを試作してベストなキャリアを作りあげています。
中村:さらに今回は、狭ピッチの繊細なはんだ付けを実現するために、これまでよりも粒子の小さな新しいはんだを採用。この実装のためだけに新たに評価して導入しているんですよ。
倉科:ICの実装が終わった後は、フレキ基板背面の指紋センサー周囲にアンダーフィルと呼ばれる絶縁性の樹脂を塗布します。これも専用の塗布機を用意し、カメラで指紋センサーの位置や高さを確認しながらICと基板のギャップをアンダーフィルで埋めています。
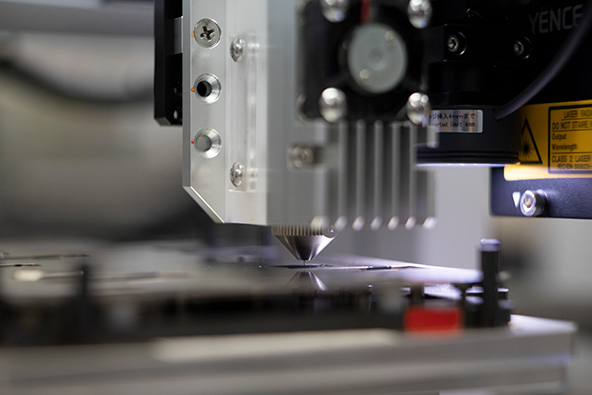
−−これは何のためにやっているんですか?
中村:静電気対策ですね。指紋センサーデバイスとフレキ基板の間にあるはんだが露出しているので、アンダーフィルで保護してあげないと冬場などに静電気がとんで故障の原因になってしまうのです。
倉科:この部分はユーザーの目に見える部分なので、最新の塗布機で高精度・高品質な作業をしています。
VAIO Zが体現するVAIOのものづくり
−−最後に製造技術、生産技術、実装、それぞれの立場から、VAIOファンの皆さんにメッセージをお願いします。
清水:新しいVAIO Zは、自社で治具や設備を設計でき、実装まで行えるVAIOの工場としての強みが最大限に活かされています。VAIOならではの上流設計で、開発から製造現場までのすべてのメンバーがしっかり議論し、多くの課題に対して最適な解を見つけられたと思っています。そういう意味で、これ以上ない「ものづくり」を実現できました。Zの経験は、引き継がれ、進化し、次のものづくりに繋がっていきます。今後もご期待ください。
手塚:VAIO Zは部署や世代の垣根を越えて、全てのメンバーが一丸となって作りあげた製品です。本当にこれまで以上に議論をしながら1つずつ問題点や懸念を解決していきました。そして今回の導入での我々のこだわりや、そのこだわりを実現するために挑戦する姿は若手メンバーたちも嫌と言うほど見てきたので、今後は引き継いでいってもらいたいですし、VAIOファンの皆さんには、今回のVAIO Zはもちろん、次の世代になっても皆さんに信じてもらえるようなモノづくりをしていくことを、約束したいと思います。
中村:これまでも難度の高い実装基板を高品質で生産できるように技術力の強化に取り組んできましたが、その成果が今回のVAIO Zで出せたことは非常に嬉しく思います。今後も、この経験をステップに、さらに高難度な技術に挑戦していきたいですね。
2021年5月27日 VAIO Pro Z発表にあたり、見出しを修正いたしました。
2021年8月4日 一部改編いたしました。
関連記事
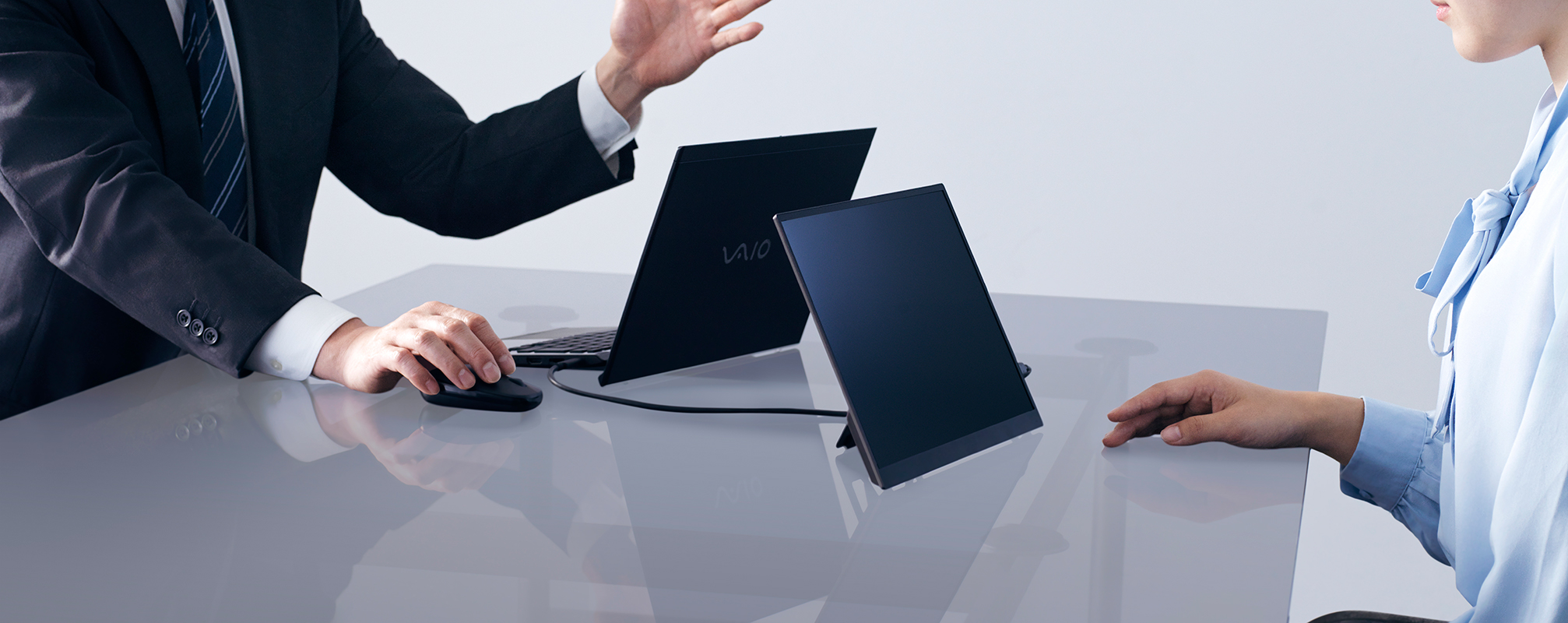
VAIO Vision+ 14・VAIO Vision+ 14P 開発者トーク Vol.1
VAIOのモバイルディスプレイがビジネスの現場にもたらす「自由な働き方と高い生産性を両立する体験」とは VAIO初のモバイルディスプレイとして開発されたVAIO Vision+TM 14・VAIO V…
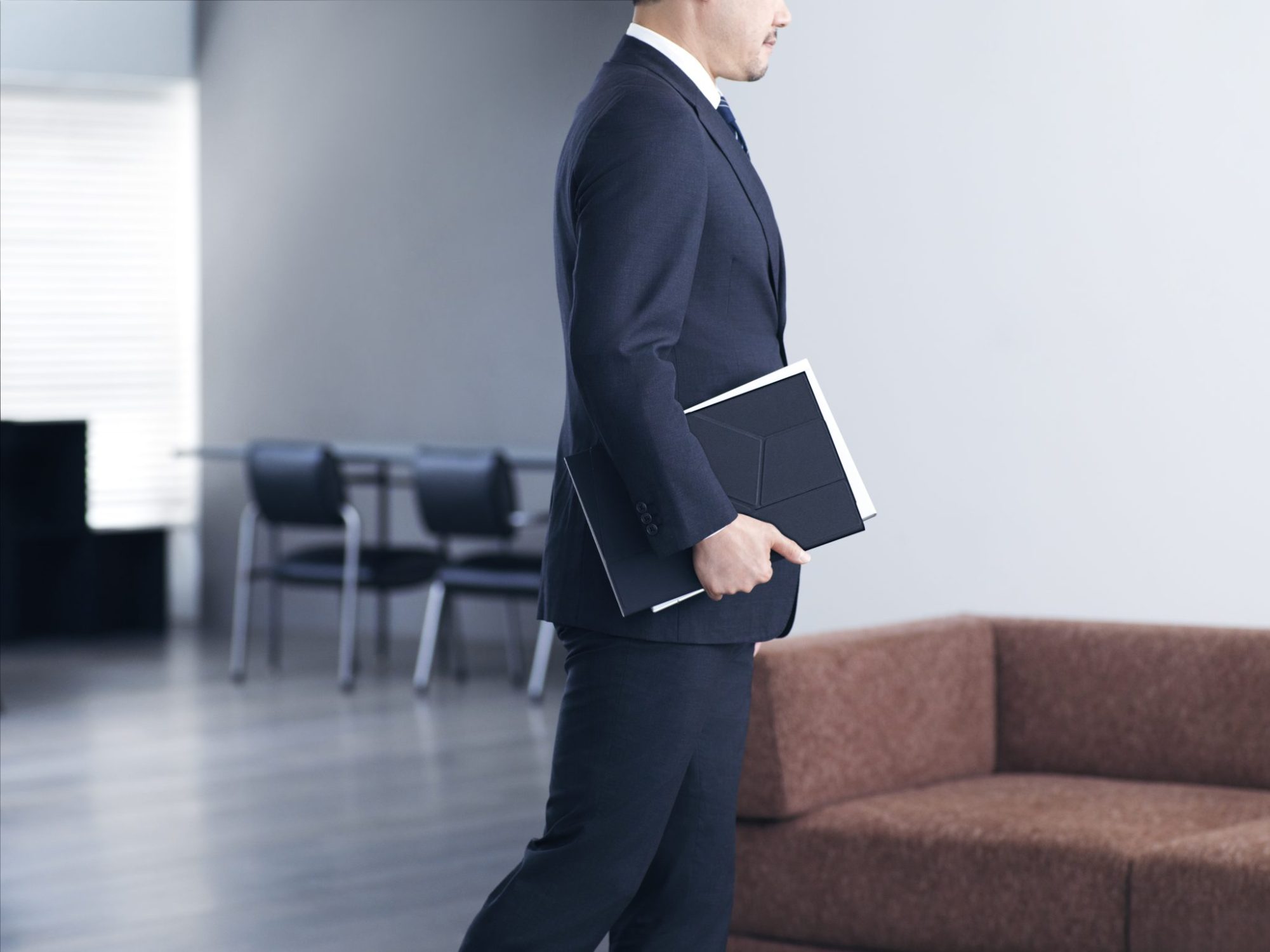
VAIO Vision+ 14・VAIO Vision+ 14P 開発者トーク Vol.2
快適な使い心地を実現するために盛り込まれたVAIOの技術とノウハウ ビジネスパーソンの「自由な働き方と高い生産性を両立する体験」を実現するべく生み出されたVAIO Vision+™ 14・VAIO V…
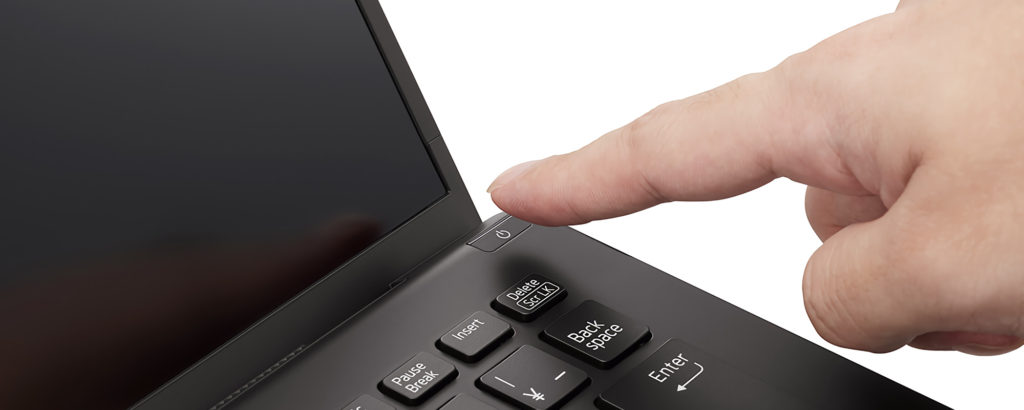
VAIO Z / VAIO Pro Z開発ストーリー Vol.8:開発者が語る「セキュリティー」使いやすさと信頼性を両立させる
VAIO Z / VAIO Pro Z開発ストーリー Vol.8:開発者が語る「セキュリティー」 VAIO Zはセキュリティーも新次元へ。2つの新型センサーを新開発したことで、使いやすさを損なうことな…
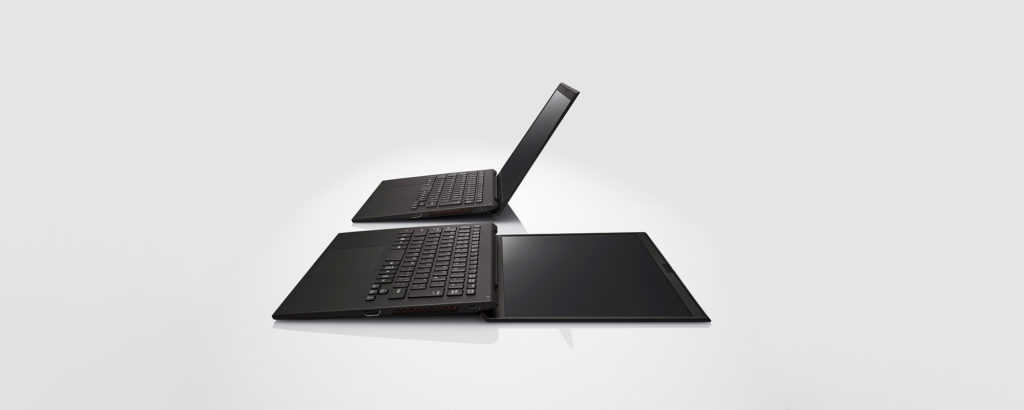
VAIO Z / VAIO Pro Z開発ストーリー Vol.7:開発者が語る「Web会議&ユーザビリティ」 新しい時代に必要なものを提供する
VAIO Z / VAIO Pro Z開発ストーリー Vol.7:開発者が語る「Web会議&ユーザビリティ」 時代は流れ、ユーザーの求めるものは次々と変わっていく。VAIOは、ユーザーに寄り沿うことで…
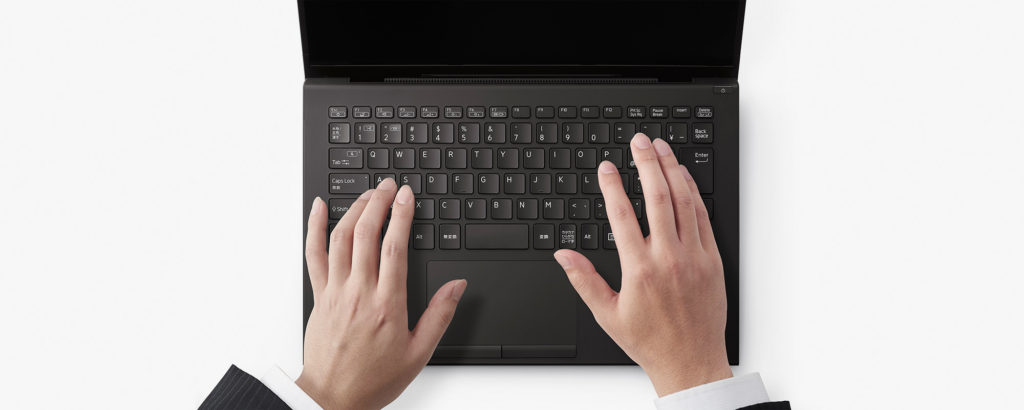
VAIO Z / VAIO Pro Z開発ストーリー Vol.6:開発者が語る「キーボード&タッチパッド」 ユーザーが直接触れる部分だからこそ
VAIO Z / VAIO Pro Z開発ストーリー Vol.6:開発者が語る「キーボード&タッチパッド」 キーボードとタッチパッドはVAIOとユーザーをつなぐ接点。それだけに一切の妥協は許されない。…
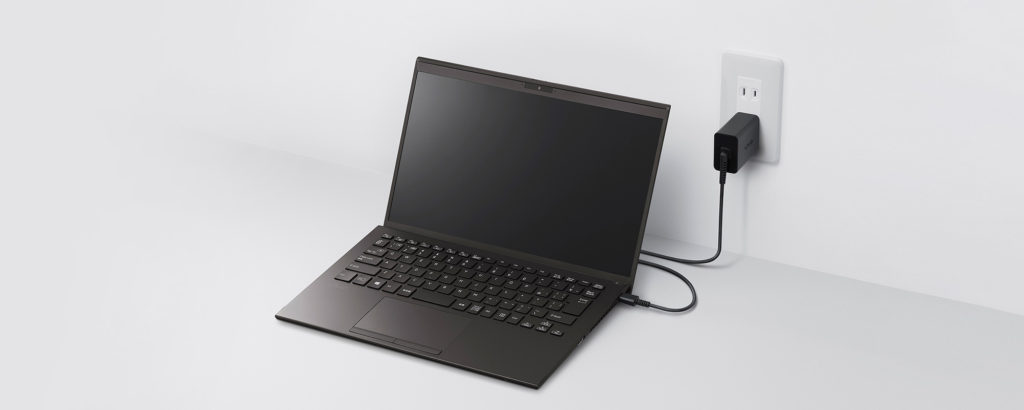
VAIO Z / VAIO Pro Z開発ストーリー Vol.5:開発者が語る「電源&バッテリー」 パフォーマンスとモビリティの融合を影で支える
VAIO Z / VAIO Pro Z開発ストーリー Vol.5:開発者が語る「電源&バッテリー」 30時間をゆうに超えるスタミナ、新開発の使いやすいACアダプター。モバイルの要である電源&バッテリー…
製品情報を見る
14.0型ワイド
個人向けモデル
法人向けモデル
インテル® Core™ プロセッサー・ファミリー
Intel Inside® 圧倒的なパフォーマンスを
Intel、インテル、Intel ロゴ、Intel Inside、Intel Inside ロゴ、Intel Atom、Intel Atom Inside、Intel Core、Core Inside、Intel vPro、vPro Inside、Celeron、Celeron Inside、Itanium、Itanium Inside、Pentium、Pentium Inside、Xeon、Xeon Phi、Xeon Inside、Ultrabook、Iris は、アメリカ合衆国および/またはその他の国における Intel Corporation の商標です。
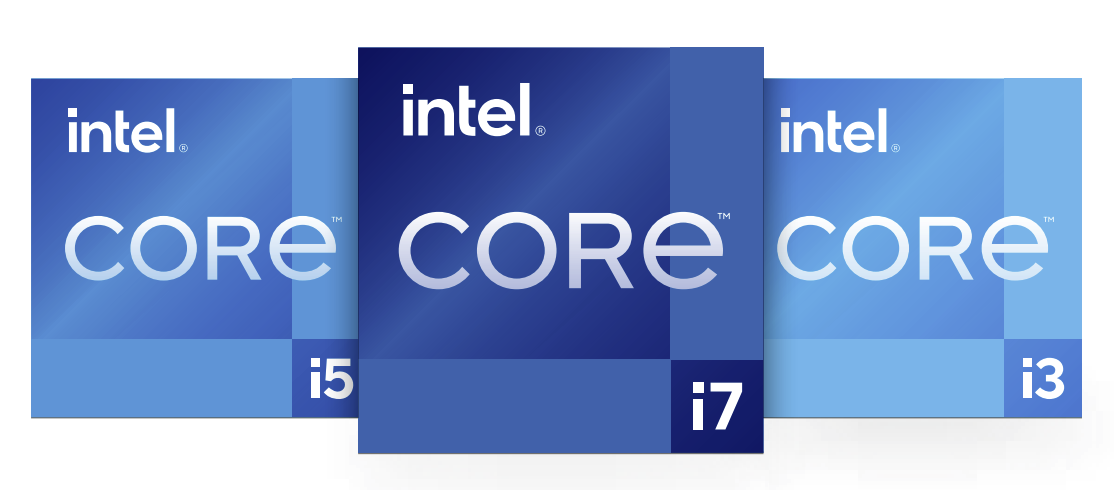